How CNC Programming Automation Boosts Productivity
In today’s fast-paced manufacturing world, every second counts, and staying competitive requires more than incremental improvements. Volume is up, and your shop is handling increasingly complex, high-precision parts, but there’s still room to optimize how tasks get done. Inefficiencies often lie within your existing processes, from initial quoting to the machining steps, and that’s where new technology comes in. CNC programming automation centralizes best practices for more consistent, higher-quality CAM programming, allowing you not only to meet but exceed customer demands with speed and precision.
By applying a future-readiness lens and leveraging technology, including AI-driven algorithms that optimize toolpath generation, shops of all sizes can unlock new levels of profitability and customer satisfaction. In addition to improved productivity, automated systems help overcome common hurdles such as integration challenges and steep learning curves through phased implementation and intuitive design. Let’s explore how CNC programming automation can strategically drive transformative productivity gains.
How to increase productivity in a CNC machine shop
Maximizing productivity in any CNC shop is about optimizing workflows, leveraging advanced tools, and minimizing manual labor. The strategy comes down to well-mapped, scalable processes combined with the strategic use of automation and AI. Consider the following key elements:
- Accurate drawings, backed by real data
Establishing a single data hub for CAM and 3D production review minimizes the guesswork and ensures that every design element is precisely captured. - Smarter planning
By aligning quoting and planning right from the design stage, you create a precision approach to resource allocation and job scheduling. This integration also enables real-time adjustments when engineering changes occur. - Automated toolpath creation
Manual toolpath creation is both time-consuming and error-prone. Automation tools use advanced algorithms and, increasingly, AI to generate various toolpaths for tasks like material removal, drilling, tapping, and finishing. Key benefits include: - Time savings
Up to a 30% to 40% reduction in programming tasks, freeing machinists to focus on higher-value work. - Improved precision
Consistent, error-free toolpaths that deliver repeatable results. - Flexibility
Rapid adaptation to design changes, even for smaller iterations.
Toolpath’s AI-driven automation solution leverages the knowledge embedded in quoting, planning, and job design processes to ensure toolpaths align with production goals, maintain tolerances, and accelerate new job opportunities. Integrated estimating and CAM management further streamline the transition from concept to production by reducing manual handoffs and ensuring that each step feeds accurate, real-time data to the next.
Check out Mastering CAM Automation: A Guide For CNC Shops for more tips and strategies to improve efficiency.
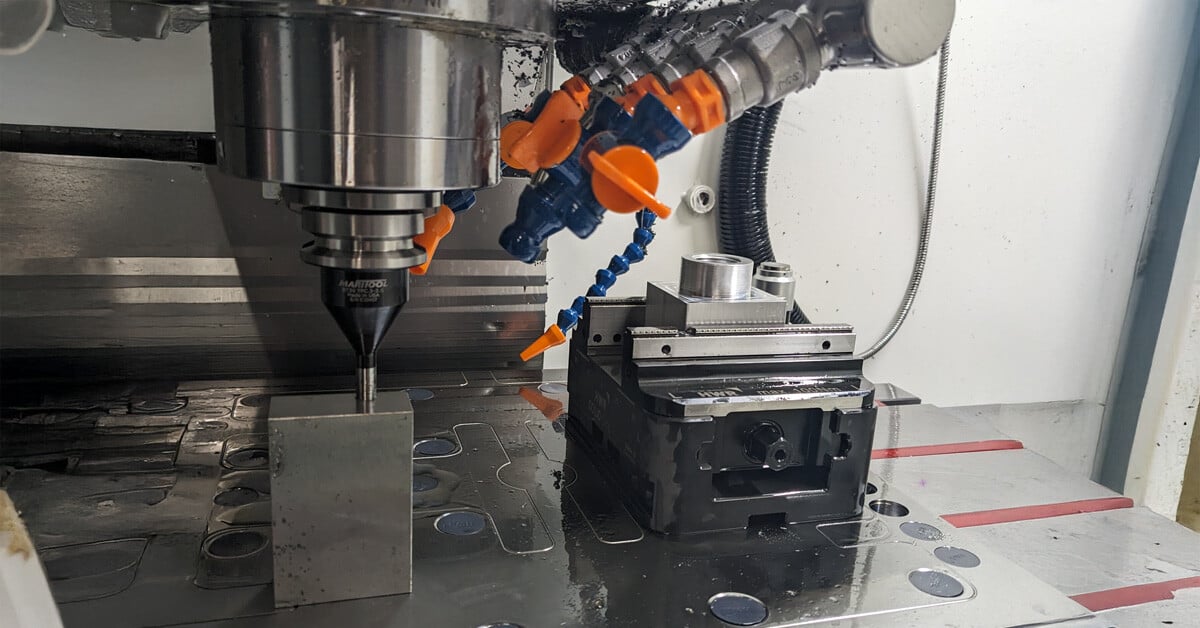
Synergy in action: Why estimating + CAM integration matters
One of the biggest friction points in many shops is the disconnect between job estimating and CAM programming. These two elements need better synchronization and alignment to avoid production bottlenecks. Toolpath leverages a modern CAM approach that integrates estimating to machining, ensuring that each phase adheres to your shop’s consistent best practices.
By automating both estimating and shop floor production management, you create a unified system where proven processes are reused for repeat orders. This synergy not only streamlines the production cycle but also enhances capacity planning and scheduling. When estimating reflects real production constraints, it’s easier to generate accurate job cost estimates and automatically create the necessary toolpaths. The result is fewer errors, improved lead times, and an automated feedback loop that minimizes manual inputs and misalignments across teams.
Turning bottlenecks into breakthroughs with Toolpath
Toolpath’s holistic approach does more than just save time; it actively transforms bottlenecks into breakthroughs. By integrating estimating, machining planning, and automated programming from historically fragmented processes, into one cohesive system, shops can manage job requests with minimal overhead.
Even though transitioning your machine shop to a stronger automation focus might initially seem daunting due to integration challenges or process disruptions, Toolpath is designed to overcome these obstacles. With user-friendly interfaces, easy-to-follow training material, and incremental adoption strategies, even shops with legacy systems can smoothly shift to a more efficient, automated environment. The ultimate payoff? More jobs completed faster, fewer errors, and a more robust bottom line.
The Toolpath Advantage
A comprehensive approach to productivity
Toolpath’s holistic AI-powered automation solution addresses the core challenges of modern machining by unifying design for machining, estimating, programming, and machine connectivity into a seamless workflow. The advantages include:
- Improved throughput
Standardized company estimation best practices ensure that each job is starting with its best foot forward. - Better scalability
Proven processes are captured and easily repeated in future work, reducing operational friction. - More consistent quality
Automated checks and AI-driven optimizations maintain high standards even with complex parts.
Tailored solutions for every shop
Recognizing that no two shops are alike, Toolpath adapts to each Team environment based on your inputs to provide the optimal fit. Whether you’re a small shop or a large-scale manufacturer, Toolpath adapts to your unique needs. By leveraging AI and automation, it amplifies your team’s expertise and gives you the tools to stay ahead in a competitive market. This all leads to:
- Quick implementation
There is minimal overhead to get started, thanks to an intuitive interface and accelerated tool library management features. - Improved collaboration
Everyone, from designers to machine operators, access the same data, from design specs to job cost analysis. - More data-driven insights
Shop managers gain actionable insights on machine utilization, process improvements, and overall performance.
Real-World Success Stories
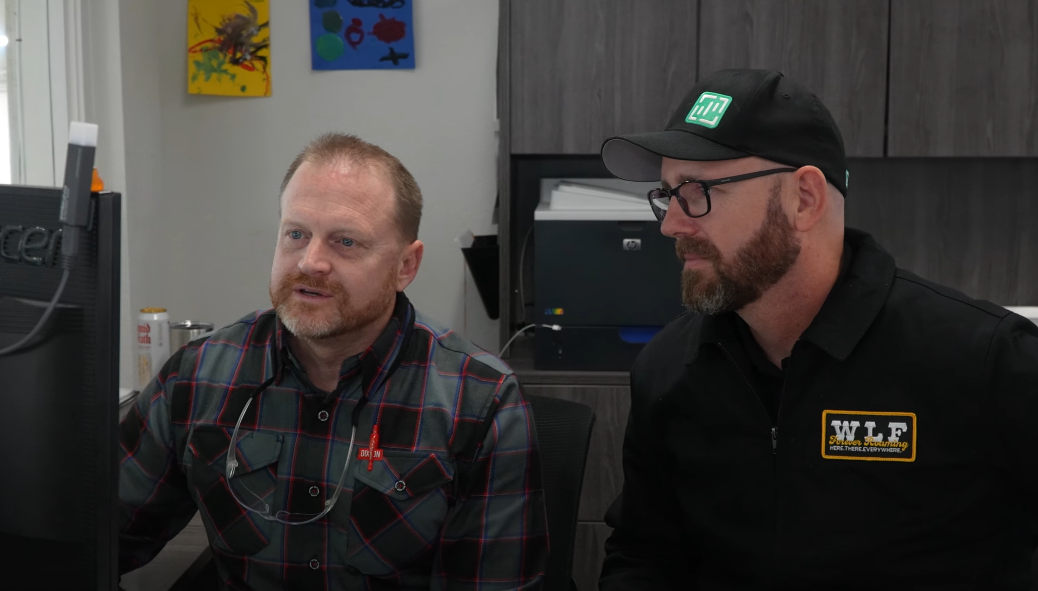
Unlocking new opportunities with integrated workflows
Take, for example, a precision machining shop specializing in low-volume, high-complexity custom parts. By employing Toolpath’s integrated automation, the shop was able to handle higher part complexity and meet greater program generation demands. Faster estimating, reduced setup times, and more accurate indexing all contributed to significant productivity gains.
Expanding capacity without adding headcount
Consider another shop focused on rapid prototyping and short-run production. With Toolpath automating up to 30% of programming tasks, streamlining hole-making, pattern repetition, and cut passes, the shop freed up valuable time for CNC machinists to tackle more critical tasks. The result was an impressive capacity boost of up to 75% with the same workforce. Manufacturers have experienced benefits such as:
- Reduced error rates, leading to fewer scrapped parts and less rework.
- Margin improvements as overhead time on quoting and programming is drastically reduced.
- Accelerated project timelines, from concept to final production.
- More consistent surface finishes and dimensional tolerances.
Ready to Transform Your CNC Operations?
Driving new capabilities in your shop doesn’t require a complete overhaul of your production environment. With Toolpath’s AI-powered automation, you benefit from a manageable, scalable solution that reduces lead times, minimizes manual tasks, and frees up your staff to tackle higher-value work.
It’s time to realize the potential of integrated quoting, CAM programming, and CNC automation. Start Your Free Trial Today and take the first step toward streamlining your operations and unlocking new levels of efficiency and precision.
Start Your Free Trial Today.
It only takes a few moments to signup.